Comprehensive Guide to Custom Helical Gear Services
1. Introduction
What Are Helical Gears?
Helical gears are cylindrical gears with angled teeth that engage gradually, offering smoother and quieter operation than spur gears. Their unique tooth design allows for higher load-carrying capacity and better efficiency, especially in high-speed applications.
Why Choose Custom Options?
At PairGears, we specialize in custom helical gear solutions, providing enhanced performance tailored to demanding industrial environments. Unlike standard gears, custom helical gears are optimized for specific conditions, offering better noise control, longer service life, and improved torque transmission.
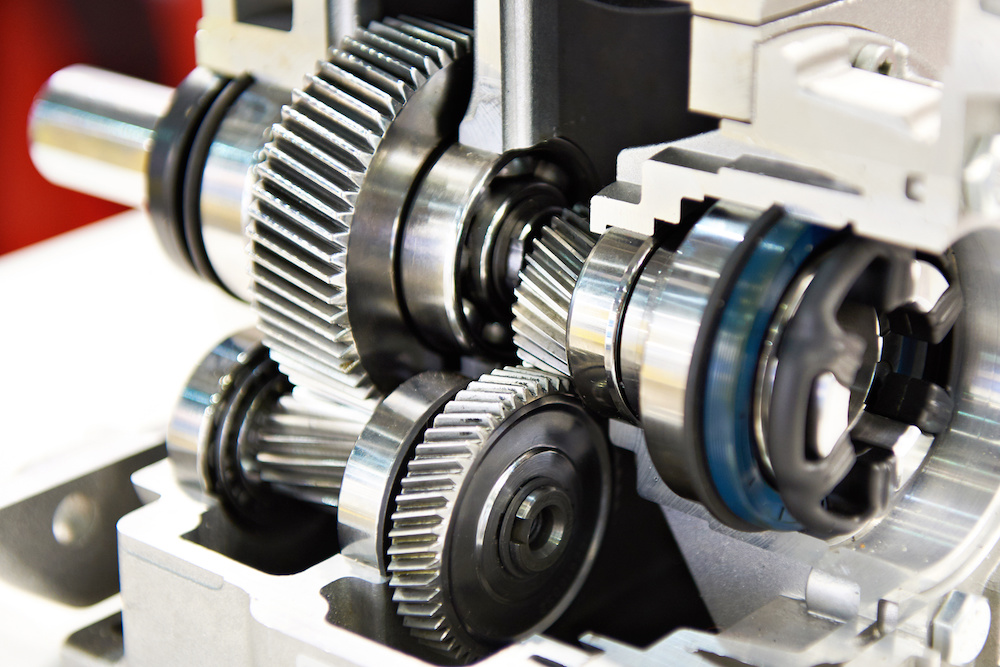
2. Advantages of Custom Helical Gears
• Smooth and Quiet Operation: Helical gears engage more gradually, reducing vibration and noise. Ideal for applications that require silent and stable transmission such as robotic arms and automotive transmissions.
• High Load Capacity: The angled tooth design provides more contact area, allowing helical gears to handle higher loads without compromising performance.
• Efficiency at High Speed: Their gradual tooth engagement reduces shock loading, making them ideal for high-speed gear systems.
• Durability and Wear Resistance: When paired with proper surface treatments like nitriding or phosphating, they offer excellent wear resistance even under harsh conditions.
• Axial Load Management: Unlike spur gears, helical gears generate axial thrust. In custom designs, this can be addressed through thrust bearings or double helical (herringbone) configurations.
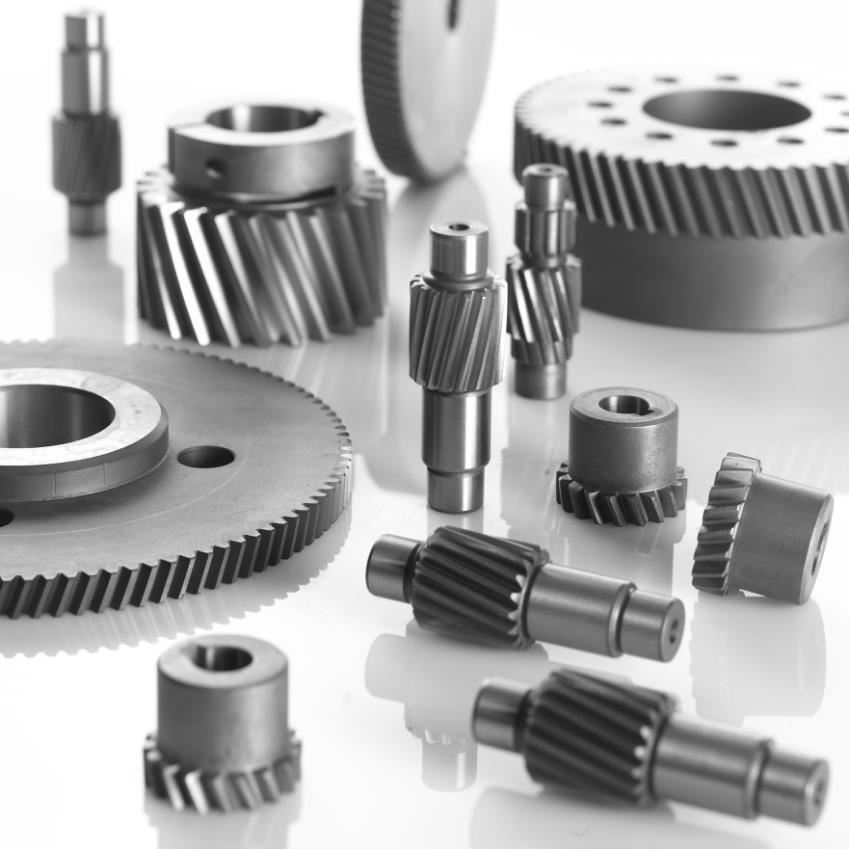
3. PairGears’ Custom Helical Gear Services
3.1 Design Customization
• Module, helix angle, pressure angle
• Face width, number of teeth
• Direction of helix (left/right-handed)
3.2 Material Options
• Alloy steels (20CrMnTi, 40Cr)
• Stainless steels (SUS304, SUS316)
• Brass and bronze for special environments
3.3 Advanced Manufacturing Techniques
• CNC machining for tight tolerance control
• Gear hobbing and shaping for precise helix profiles
• Gear grinding to achieve low surface roughness and noise
• Heat treatment for optimal hardness and fatigue resistance
3.4 Surface Treatments
• Nitriding
• Phosphating
• Chrome plating (Enhance corrosion and wear resistance)
3.5 Quality Assurance and Fast Delivery
• In-house inspection: hardness, concentricity, tooth profile
• ISO-certified process and third-party reports
• Fast lead time with scalable production for batch and OEM orders

4. Key Technical Considerations
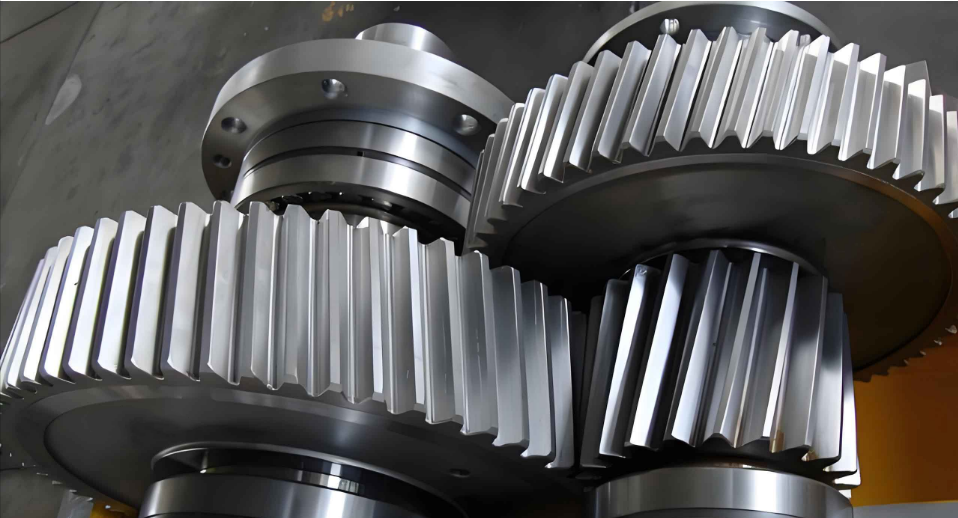
4.1 Helix Angle Selection
A higher helix angle increases tooth contact but also axial load. Typical values range from 15° to 30°, depending on application and shaft distance. Read more on gear geometry impact.
4.2 Precision Grinding
Custom helical gears often require profile grinding to reduce transmission error, especially for applications such as aerospace and robotics.
4.3 Noise and Vibration Control
By adjusting face width and tooth profile modification, PairGears ensures better dynamic performance for quiet transmission.
4.4 Gear Alignment
Because of axial forces, proper alignment and mounting tolerance are critical. We provide complete technical drawings and engineering support.
5. Applications of Custom Helical Gears
• Automotive Transmission Systems
Used in gearboxes for smooth shifting and noise reduction.
• Robotics and Automation
Precise motion control in servo gearboxes and rotational actuators.
• Aerospace Engineering
Used in turbines, actuators, and flap control systems.
• Industrial Machinery
High-speed pumps, compressors, and conveyor systems.
• Agricultural Equipment
Combine harvesters, high-torque gearboxes, and rotary tillers.
• Renewable Energy
Wind turbine gearboxes using hardened helical stages.
6. Case Studies: Real-World Applications by PairGears
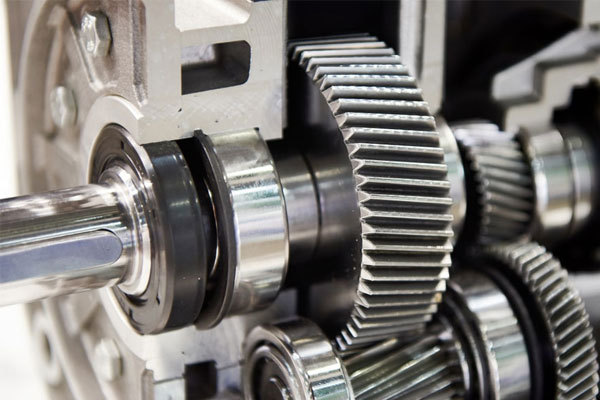
6.1 Automotive Industry
We provided low-noise helical gears to a European EV manufacturer, improving energy efficiency by 12%.
6.2 Robotics Sector
Our ground helical gears enhanced repeatability in 6-axis robotic arms for an automation client.
6.3 Wind Energy OEM
Custom hardened gears were used in a turbine reducer box, withstanding heavy torque and variable load cycles.
7. FAQ
Q1: What’s the typical helix angle you offer?
A1: Standard angles are 15°, 20°, and 30°, but custom angles are available based on design requirements.
Q2: Can you manufacture double helical gears (herringbone)?
A2: Yes, we offer herringbone gears with zero axial load design.
Q3: Are your gears certified?
A3: Yes, all gears are produced under ISO 9001:2015 quality standards.
Q4: What industries do you serve?
A4: Automotive, energy, machinery, aerospace, agriculture, and more.
8. Start Your Custom Gear Project with PairGears
Whether you need custom helical gears for power transmission or precision components for automation, PairGears is ready to help.Contact us today to start your project.
Should you have any questions or require further assistance, please do not hesitate to contact our engineer: ben@pairgears.com.