This document outlines the metrics used to define and track defect levels during production, ensuring a standardized approach for assessing product quality at various stages of the manufacturing process.
Leading Through Quality Control
Strict Quality Control
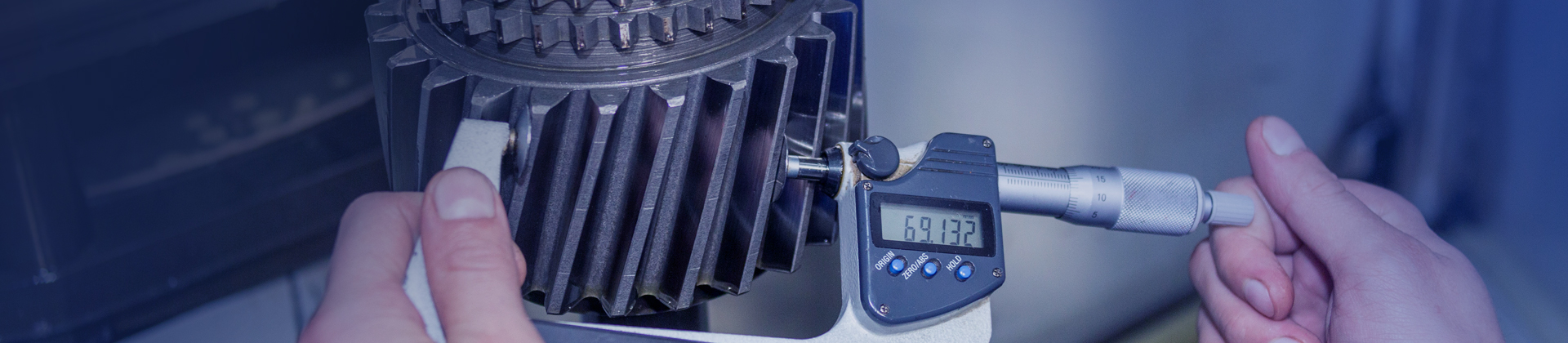
Home / Quality Control
PairGears always prioritizes product quality, understanding that high-quality products are key to earning customer trust. Therefore, PairGears implements strict quality control measures at every stage to ensure that each product meets or even exceeds customer expectations.
Quality Management Documents
Comprehensive Quality Management System
IATF 16949 Quality Management Standard
PairGears relies on the IATF 16949 quality management system, covering every stage from raw material procurement to production processing, process inspection, and final product inspection. Through comprehensive quality management, every step is ensured to meet stringent quality standards.
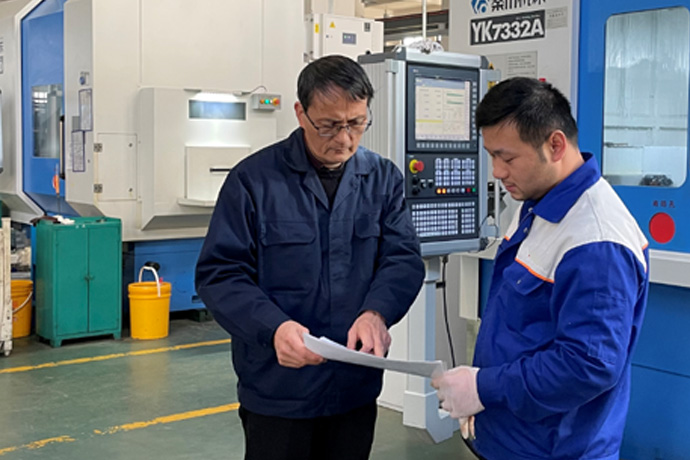
Advanced gear and test equipment
High-Precision Testing Equipment
PairGears is equipped with advanced gear and material testing equipment, including three-coordinate measuring machines, gear testing centers, material hardness testers, metallographic analyzers, and material spectrometers. These devices enable high-precision testing of products and materials, ensuring that every detail meets quality requirements.
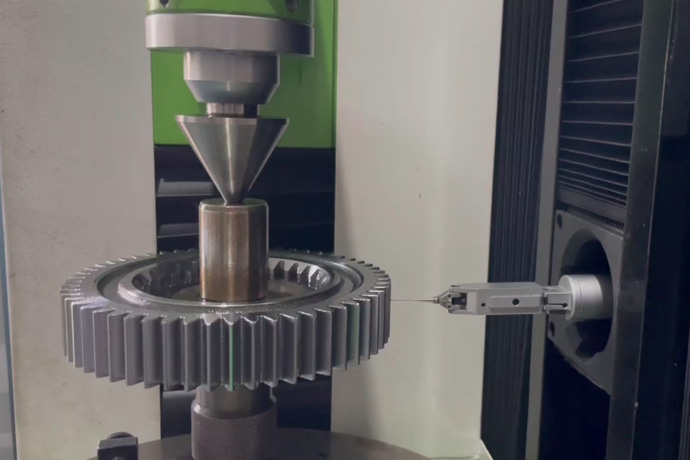
Detailed Process Management
Strict Process Control
During production, PairGears implements strict process controls, with each process step meticulously recorded and closely monitored. By optimizing the process flow, production efficiency is improved while ensuring product consistency and stability.
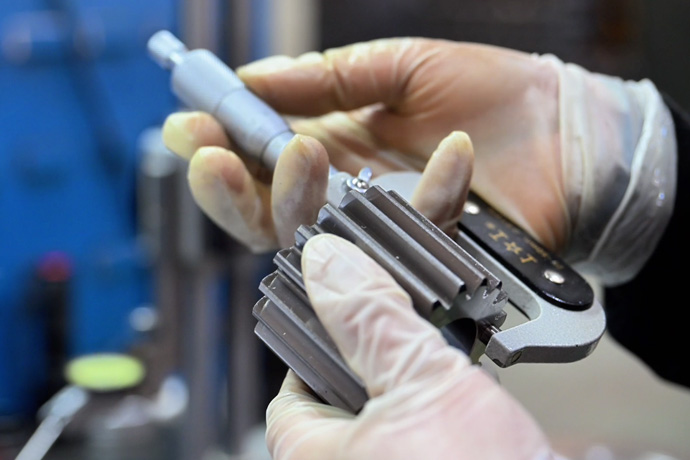
Strict Perpendicularity testing standards
Shaft Perpendicularity Testing
After heat treatment, shafts may experience some bending deformation. Perpendicularity testing can promptly identify and correct bending phenomena, ensuring the accuracy and stability of transmission and extending the lifespan of gearboxes.
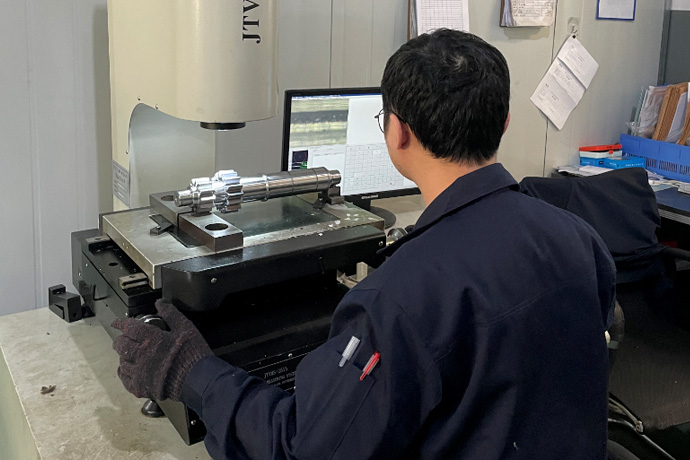
Strict hardness testing standards
Gear Hardness Testing
The gear is finished after the tooth shape machining, heat treatment is required to increase the surface hardness of the gears. The surface hardness must meet design requirements to ensure that the gears can withstand high loads and high-speed operation without deformation or surface wear. Hardness testing also helps optimize the heat treatment process, improving gear hardness and wear resistance, thus extending the service life of the gears.
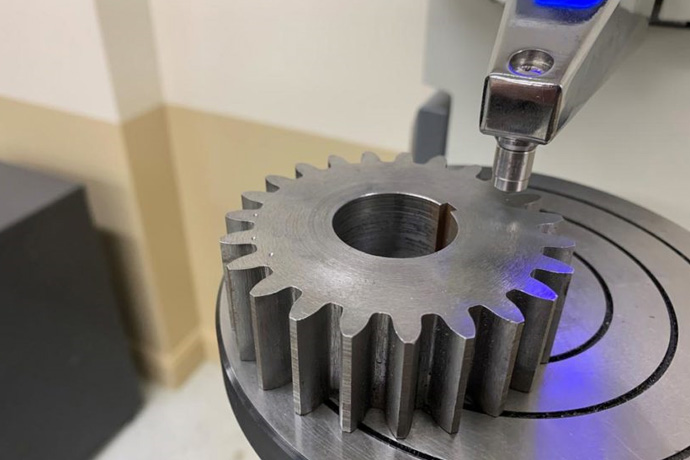
Ensure quality meets design requirements
Metallographic Analysis of Gear Internal Materials
Metallographic analysis detects the uniformity of the internal structure of gears, identifying any defects or foreign materials, and evaluates the manufacturing process's conformity to ensure quality meets design requirements.
The results also provide reference data for gear design and heat treatment process optimization, aiding in the selection of materials, heat treatment parameters, and process flows to enhance gear performance and longevity.
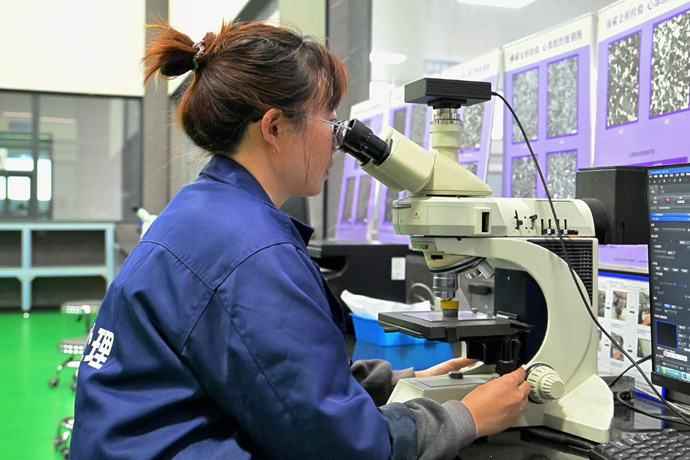
Adhere to the principle of continuous improvement
Continuous Improvement and Optimization
PairGears adheres to the principle of continuous improvement, enhancing product quality through ongoing technological innovation and process optimization. Employees are encouraged to actively participate in quality improvement activities, collectively advancing the company's quality standards.
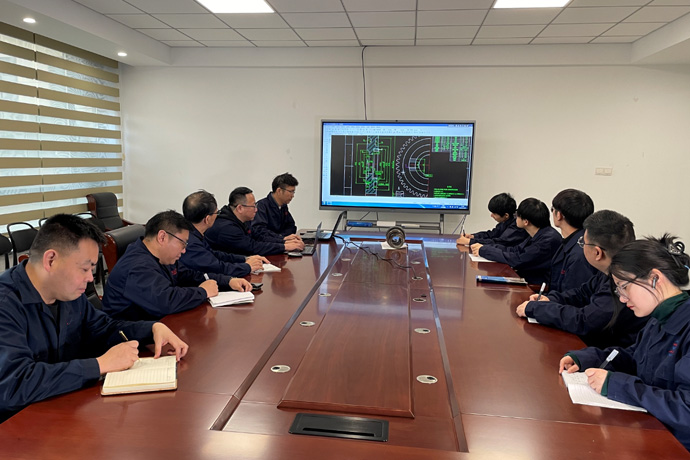
PairGears' quality control standards not only comply with the IATF 16949 international standard but also exceed the industry's general requirements. A detailed quality control manual has been established, which all employees must strictly follow, ensuring that every stage from design to production meets the highest standards.
Quick Quote
Minimum Order for Precision Gears is 1 Piece
Imagine what it would be like to have a place that could bring your ideas to life. PairGears doesn't just provide products, we provide the possibility to make your dreams come true. Every innovation starts with a simple idea, and we're here to help you explore those endless possibilities. Click below to take the first step in your customization journey. Let’s uncover the mystery behind customized services and discover how to turn your unique ideas into concrete practice. Because at PairGears, we believe every idea deserves to be crafted with care.Quick Quote
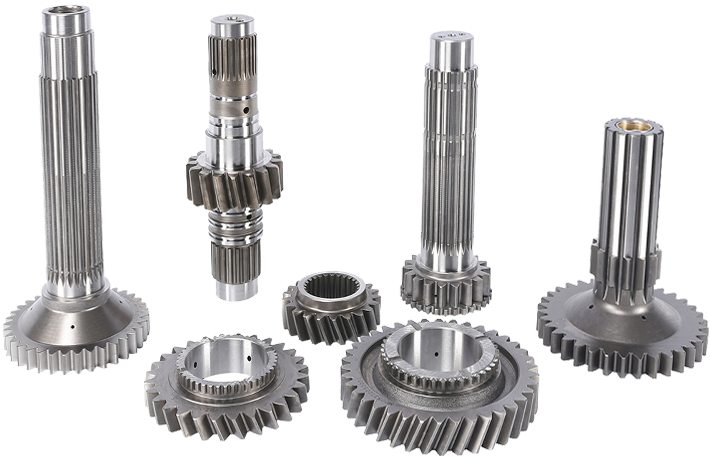
Partner
Committed to Our Customers
Join Our Distributors
Are you looking for a partnership with huge market potential and generous profit margins? As our distributor, you will receive comprehensive market support, high-quality product resources, and professional business training. Contact us now to learn more about becoming our distributor and start your journey to success!
- Name
- Tel
- *Title
- *Content