Discovering the Superior Performance and Applications of Ductile Iron in SAE J434
Ductile Iron, also known as spheroidal or nodular iron, is described as cast iron in which the graphite is present as spheroids, instead of flakes as in gray iron or temper carbon nodules as in malleable iron. Ductile iron is most popular metal material.
Reference Casting Standards:
SAE J434: Automotive Ductile (Nodular) Iron Castings
Ductile Iron castings can be produced in Casting Quality
Industrial:
Sand Casting
Shell Casting
Lost Form Casting
Ductile iron standard grades in SAE J434
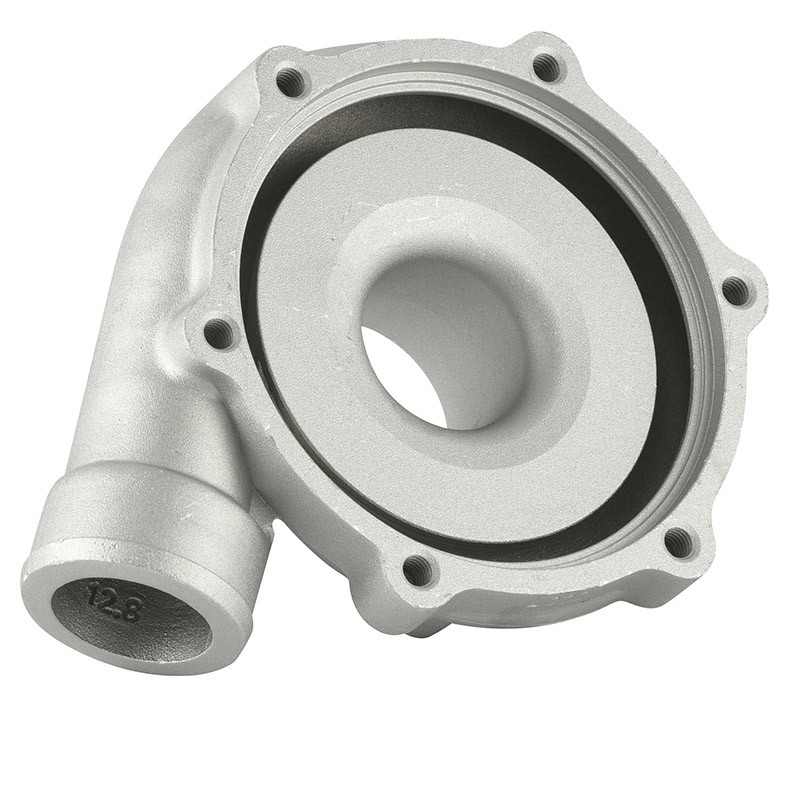
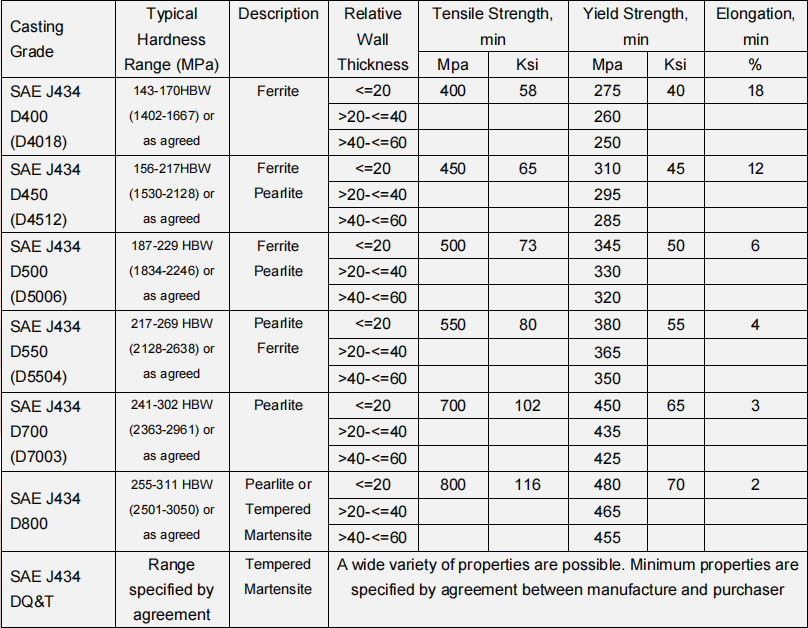
SAE J434 Ductile Iron Heat treatment requirement:
Generally the heat treatment of castings and specimens in SAE J434 in order to meet the hardness or
mechanical property requirements is permissible only with the express approval of the casting purchaser.
But the typical microstructures of the grade of ductile iron as follows (for reference only):
D400(D4018) is a ferritic ductile iron most commonly made by annealing.
D450 (D4512) is ferritic ductile iron supplied either as cast or heat treated.
D500 (D5006) is ferritic-pearlite ductile iron supplied either as cast or heat treated.
D550 (D5504) is pearlitic-ferritic ductile iron supplied either as cast or heat treated.
D700 (D7003) is either as cast or qir quenched to a specified hardness range.
D800 is either as cast or air or liquid quenched and tempered to a specified hardness range.
DQ&T is liquid quenched and tempered grade.
SAE J434 Microstructure:
The graphite component of the microstructure shall consist of at least 80% spheroidal graphite conforming
to types I and II (per ASTM A247)
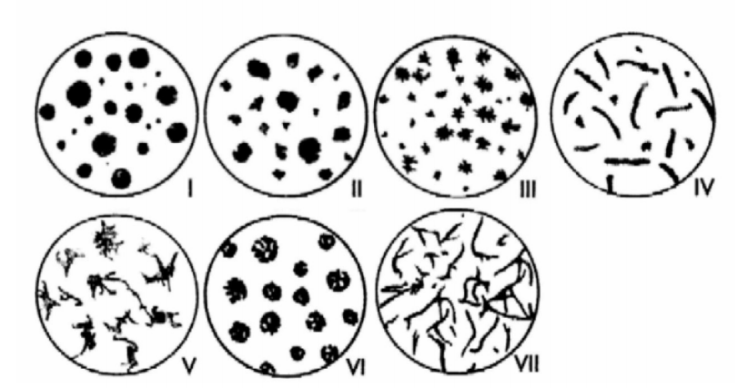
The matrix microstructure shall consist of ferrite, ferrite and pearlite, pearlite, tempered pearlite, or tempered martensite, or a combination of those.

D400 Typical Matrix Microstructures
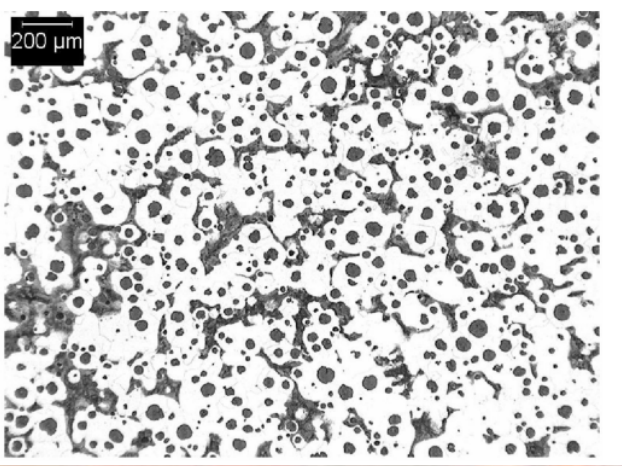
D450 Typical Matrix Microstructures
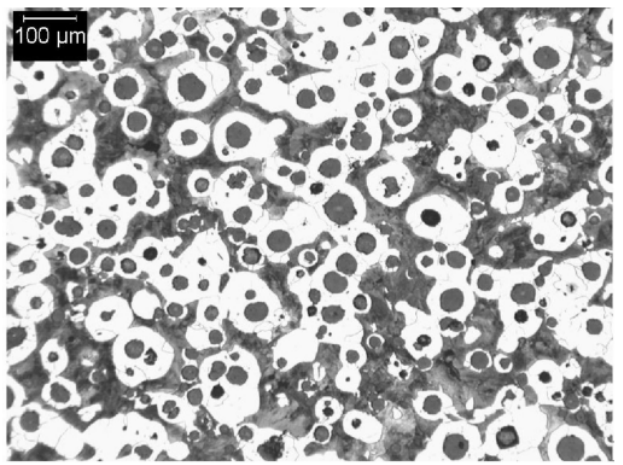
D500 Typical Matrix Microstructures
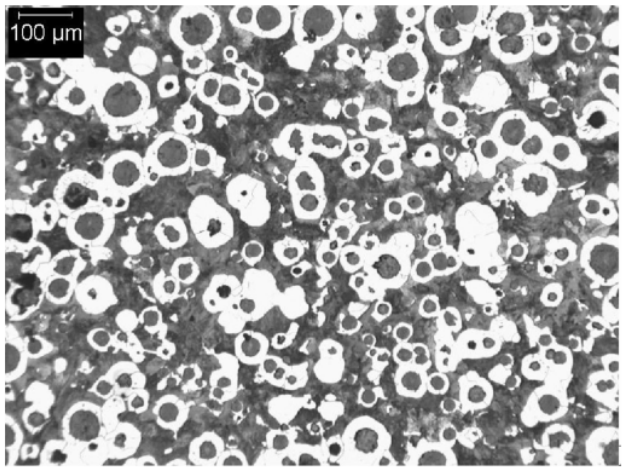
D550 Typical Matrix Microstructures
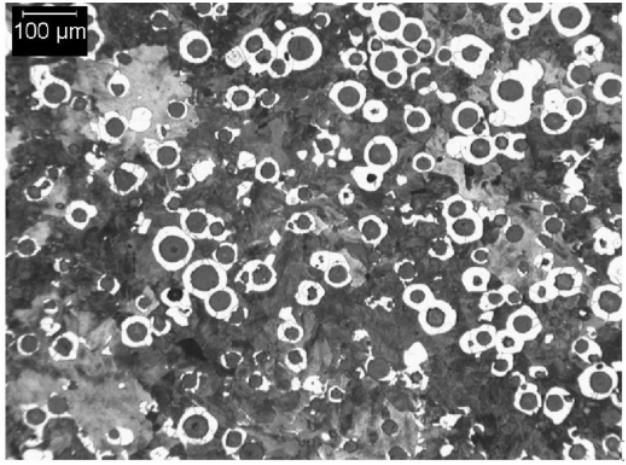
D700 Typical Matrix Microstructures
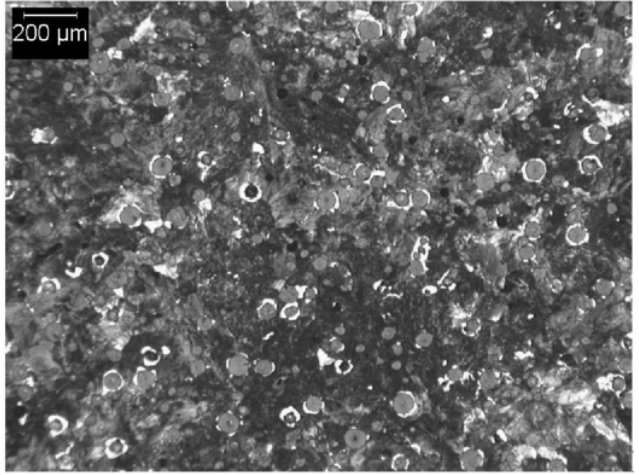
D800 Typical Matrix Microstructures
Chemical Composition in SAE J434 ( for information only): The typical chemical composition of
unalloyed iron generally confirms to following range. The spheroidal graphite structure is produced by
alloying the molten iron with small amounts of one or more elements such as magnesium or cerium. The
matrix microstructure may be controlled by addition of other alloying elements, such as: copper, tin, nickel,
chromium and molybdenum.
Carbon: 3.20-4.10%
Silicon: 1.80-3.00%
Manganese: 0.10-1.00%
Phosphorus: 0.050% max
Sulfur: 0.035% max
Magnesium: 0.025-0.060%
Typical un-notched Charpy impact energy properties are from low residual element content iron,
impact values are affected by microstructure and section size:
Grade
|
TYPICAL IMPACT VALUE(For information only)
|
|
JOULES
|
FT-LBS
|
|
SAE J434 D400(D4018)
|
120
|
90
|
SAE J434 D450(D4512)
|
80
|
60
|
SAE J434 D500(D5006) | 54 | 40 |
SAE J434 D550(D5504) | 40 | 30 |
SAE J434 D400(D4018) | 27 | 20 |
SAE J434 Ductile Iron Typical Casting Application
Machinery, valve, truck, railway, gearbox, flywheels etc.
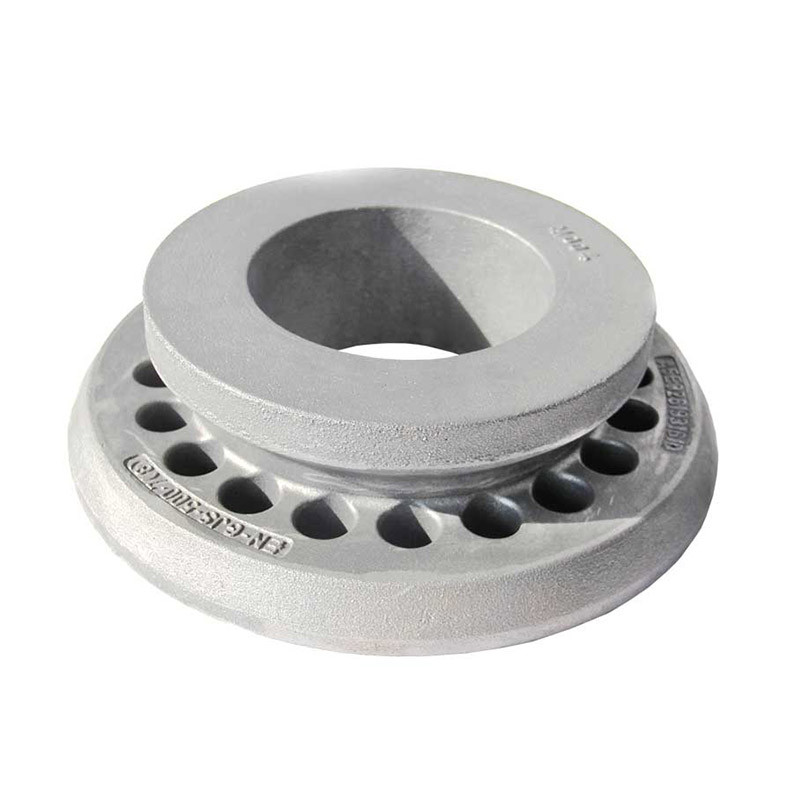
D400 (D4018 is used in moderately stressed parts
requiring high ductility and good machinability.
D450 (D4512) and D500 (D5006) are used for
moderately stressed parts where machinability is less
important.
D550 (D5504) is used for more highly stressed parts.
D700 (D7003) and D800 are used where high strength
and/or improved wear resistance are required and where
selective hardening is to be employed.
DQ&T is used where the uniformity of a heat treated
material is required to control the range of mechanical
properties or machinability.