Exploring the Benefits and Limitations of Powder Metallurgy Gears
Introduction
PairGears is a leading manufacturer of high-quality gears, specializing in innovative solutions to meet diverse industry needs. Our expertise encompasses various gear manufacturing techniques, including the advanced process of powder metallurgy (PM).
In this blog, we will explore the PM process, its advantages and disadvantages, and its applications, particularly in the automotive sector.
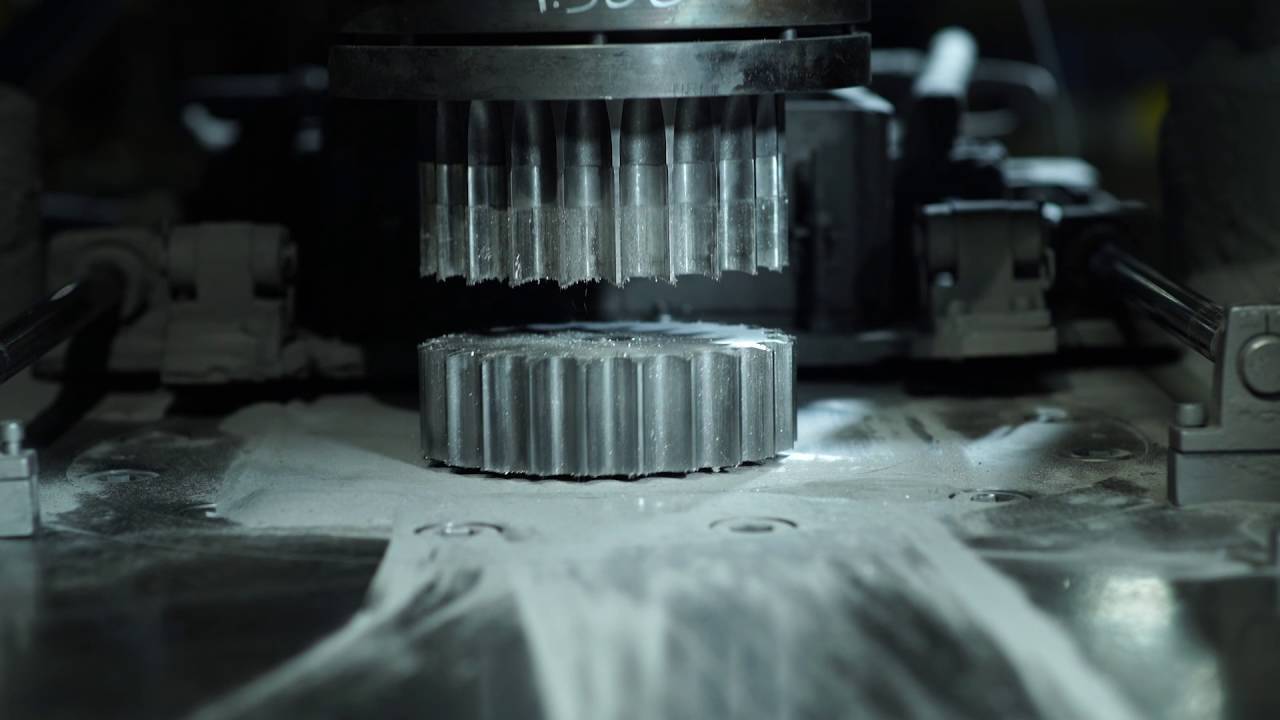
Understanding Powder Metallurgy
Powder metallurgy is a manufacturing process that involves three primary steps:
1. Mixing Metal Powders: Carefully selected metal powders are blended to achieve the desired material properties.
2. Compacting: The mixed powders are compressed into a specific shape using high pressure, forming a "green" compact.
3. Sintering: The compacted shape is heated under controlled conditions, causing the particles to bond and resulting in a solid, dense metal part.
This process allows for the production of components that are near-net shape, often requiring minimal machining.
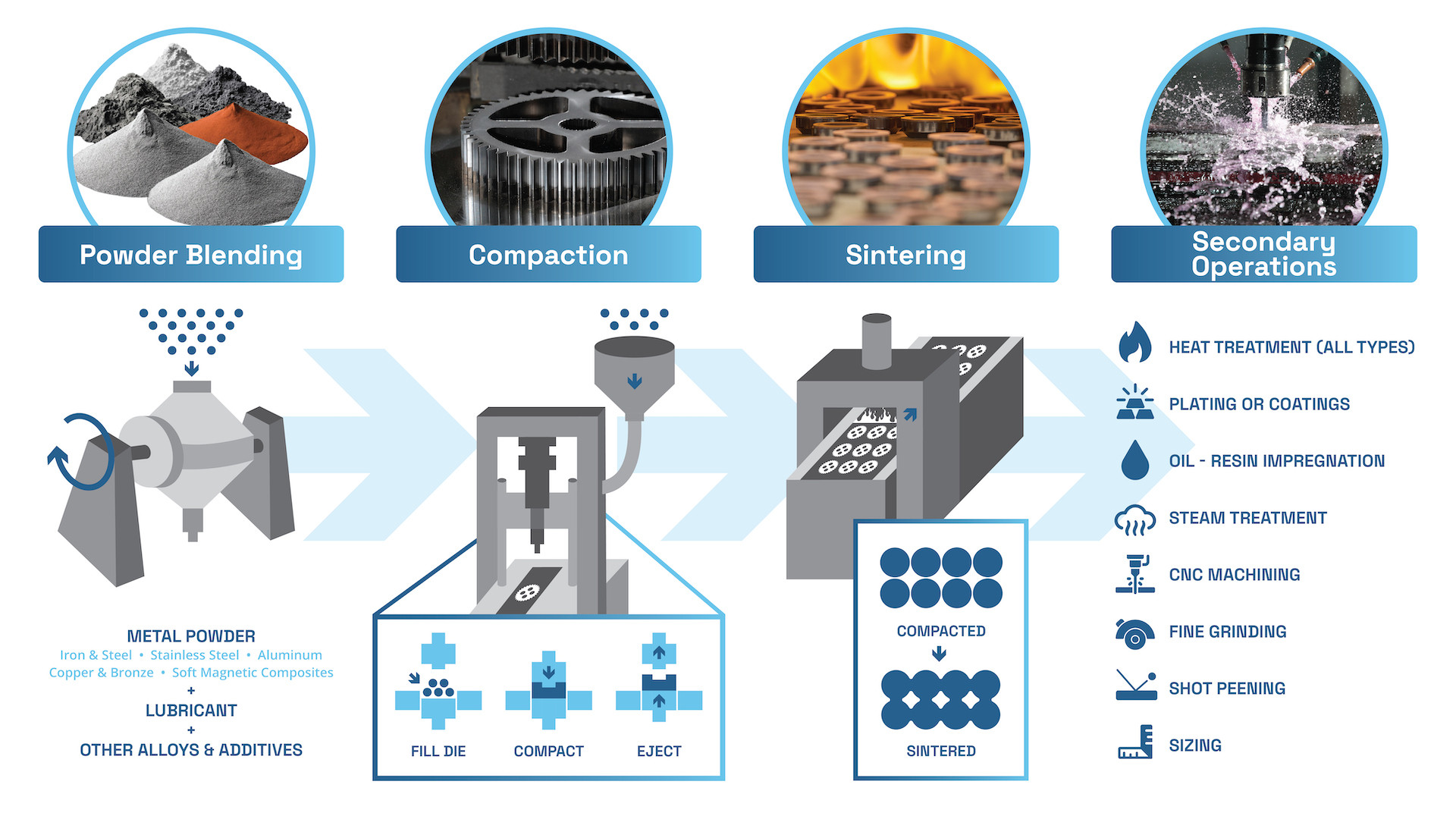
Advantages of Powder Metallurgy Gears
• Cost-Effectiveness: PM gears are generally more economical in large-scale production due to reduced material waste and energy consumption.
• Material Efficiency: The PM process minimizes waste, as excess powder can often be recycled.
• Design Flexibility: PM allows for the creation of complex shapes and unique material compositions, enabling tailored properties for specific applications.
• Self-Lubrication: The inherent porosity of PM gears permits impregnation with lubricants, resulting in self-lubricating components that reduce maintenance requirements.
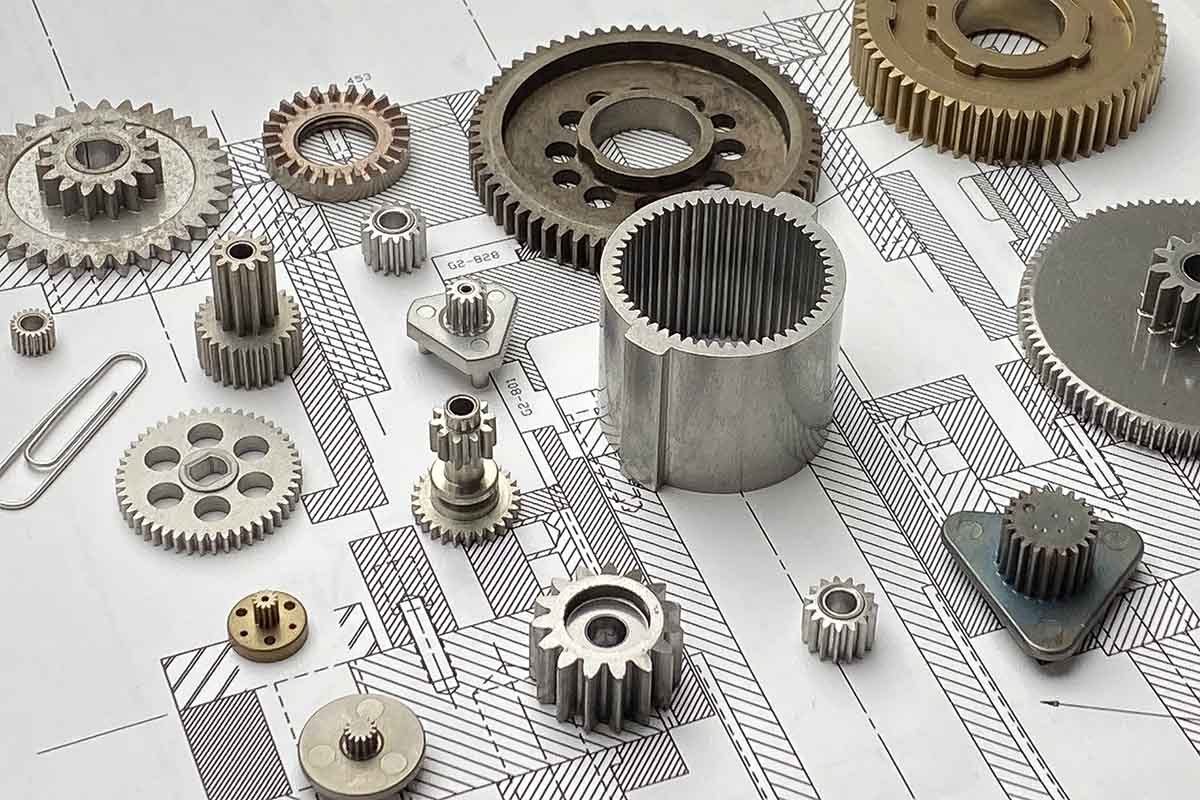
Disadvantages of Powder Metallurgy Gears
• Mechanical Strength: PM gears may exhibit lower tensile strength and fatigue resistance compared to wrought or forged gears, limiting their use in high-stress applications.
• Dimensional Limitations: The size of PM gears is constrained by the capabilities of pressing equipment and the need to maintain uniform density.
• Surface Finish: While PM produces near-net shapes, additional machining may be required to achieve precise tolerances or surface finishes.
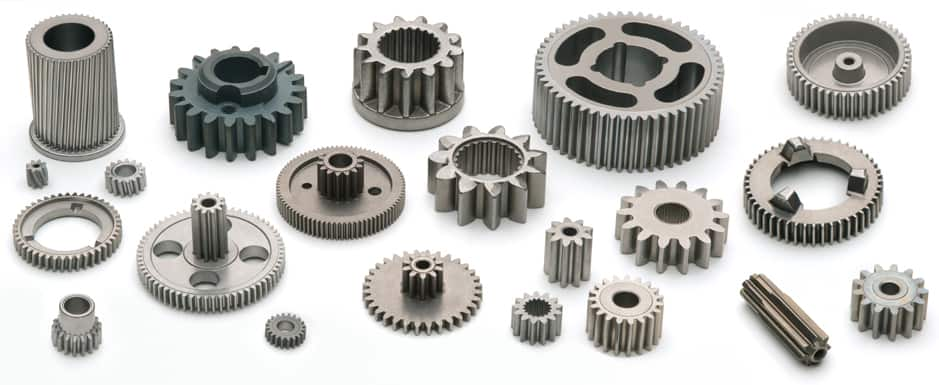
Applications of PM Gears in the Automotive Industry
The automotive sector extensively utilizes PM gears due to their cost efficiency and performance characteristics. Common applications include:
• Engine Components: Sprockets, pulleys, and oil pump gears benefit from the precision and material properties achievable through PM.
• Transmission Systems: Gear shift components manufactured via PM offer reliable performance with reduced manufacturing costs.
• Turbocharger Assemblies: PM allows for the production of complex geometries essential for efficient turbocharger operation.
These applications highlight the versatility of PM in meeting the stringent demands of automotive engineering.
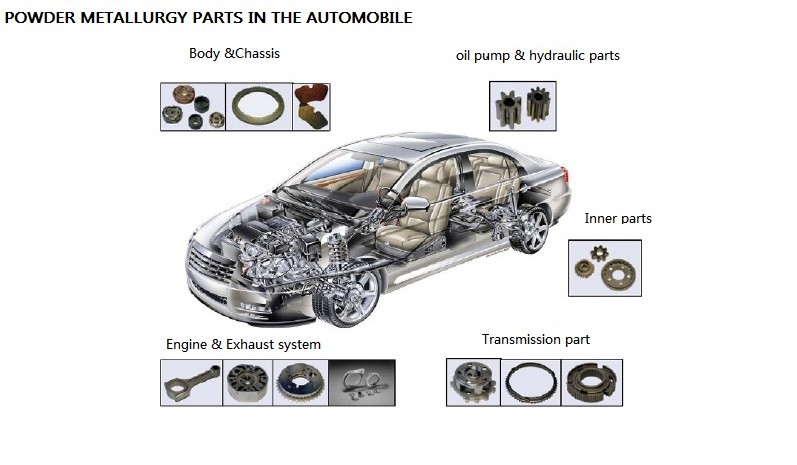
PairGears' Expertise in Powder Metallurgy
At PairGears, we leverage the advantages of powder metallurgy to deliver high-quality gear solutions tailored to our clients' needs. Our capabilities include:
• Custom Material Blending: We develop specific alloy compositions to achieve desired mechanical properties.
• Precision Compaction: Utilizing advanced pressing techniques ensures uniform density and structural integrity.
• Controlled Sintering: Our state-of-the-art sintering processes result in components with optimal strength and durability.
For more information on our PM gear offerings, please visit our products page.
Conclusion
Powder metallurgy presents a viable alternative to traditional gear manufacturing methods, offering benefits such as cost savings, design flexibility, and self-lubrication. However, considerations regarding mechanical strength and size limitations are essential when selecting PM gears for specific applications.
PairGears remains committed to providing innovative gear solutions through advanced manufacturing techniques like powder metallurgy. Our dedication to quality and customer satisfaction ensures that we meet the evolving demands of various industries.
Should you have any questions or require further assistance, please do not hesitate to contact our engineer: ben@pairgears.com.
Sources:
• Machine Design: Powder metallurgy gears gain strength and viability
• Powder Metallurgy Review: Powder Metallurgy: The process and its applications