Understanding Gear Finishing: Gear Lapping, Honing & Grinding
Introduction
At PairGears, a trusted name in precision gear manufacturing, we specialize in producing high-performance gears for agricultural, automotive, and industrial machinery. With decades of experience and advanced processing capabilities, our team ensures every gear achieves optimal precision and durability. To accomplish this, we rely on advanced finishing techniques—namely gear grinding, gear honing, and gear lapping—each of which plays a vital role in the gear production lifecycle.
In this blog, we’ll compare and contrast these three finishing processes and explain how we integrate them at PairGears to ensure outstanding gear performance.
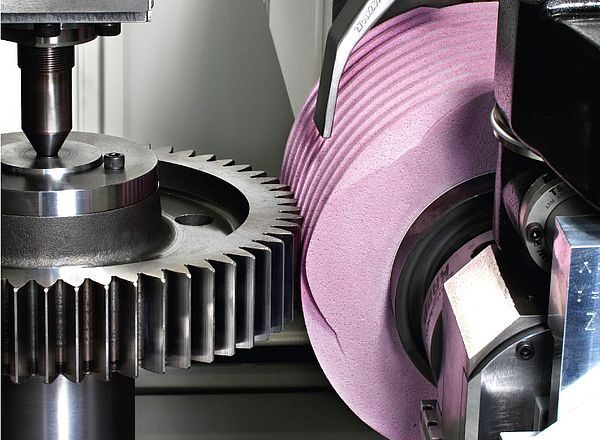
Gear Grinding: Shaping Precision
Gear grinding is often employed after heat treatment to refine tooth shape, remove distortion, and achieve high dimensional accuracy. Using abrasive grinding wheels, this process removes excess material with high cutting force, making it ideal for semi-finished or fully hardened gears.
• Purpose: High-precision gear tooth profile, efficient batch processing
• Cutting Force: High (abrasive control with grinding wheel)
• Stage: Semi-finishing or finishing stage
Learn more: Detailed Description of Gear Grinding Process
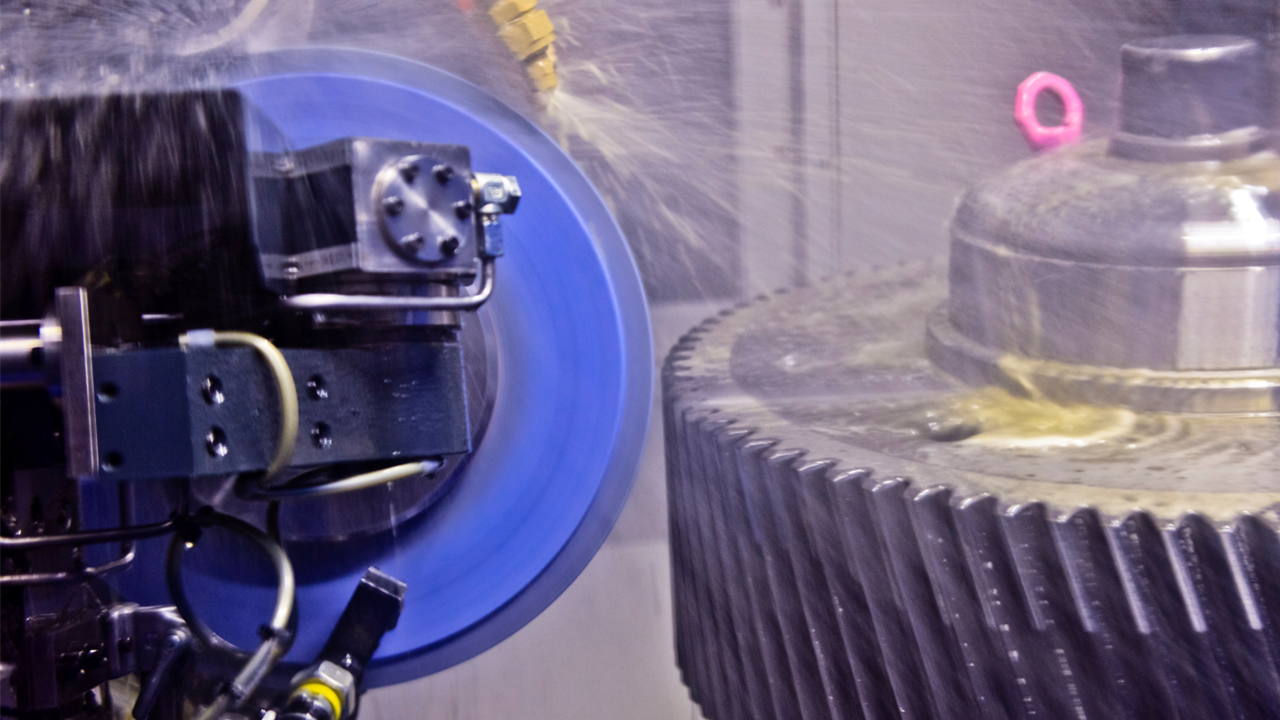
Gear Honing: Improving Texture and Reducing Noise
Honing uses a specialized honing tool to refine the microstructure of the gear tooth surface, improve texture, remove burrs, and reduce noise. This process operates with moderate cutting pressure and is excellent for enhancing surface finish post-grinding.
• Purpose: Microstructure enhancement, burr removal, noise reduction
• Cutting Force: Medium to low (oil stone contact under pressure)
• Stage: Final micro-adjustment
Dive deeper: Enhancing Gear Performance Through Honing
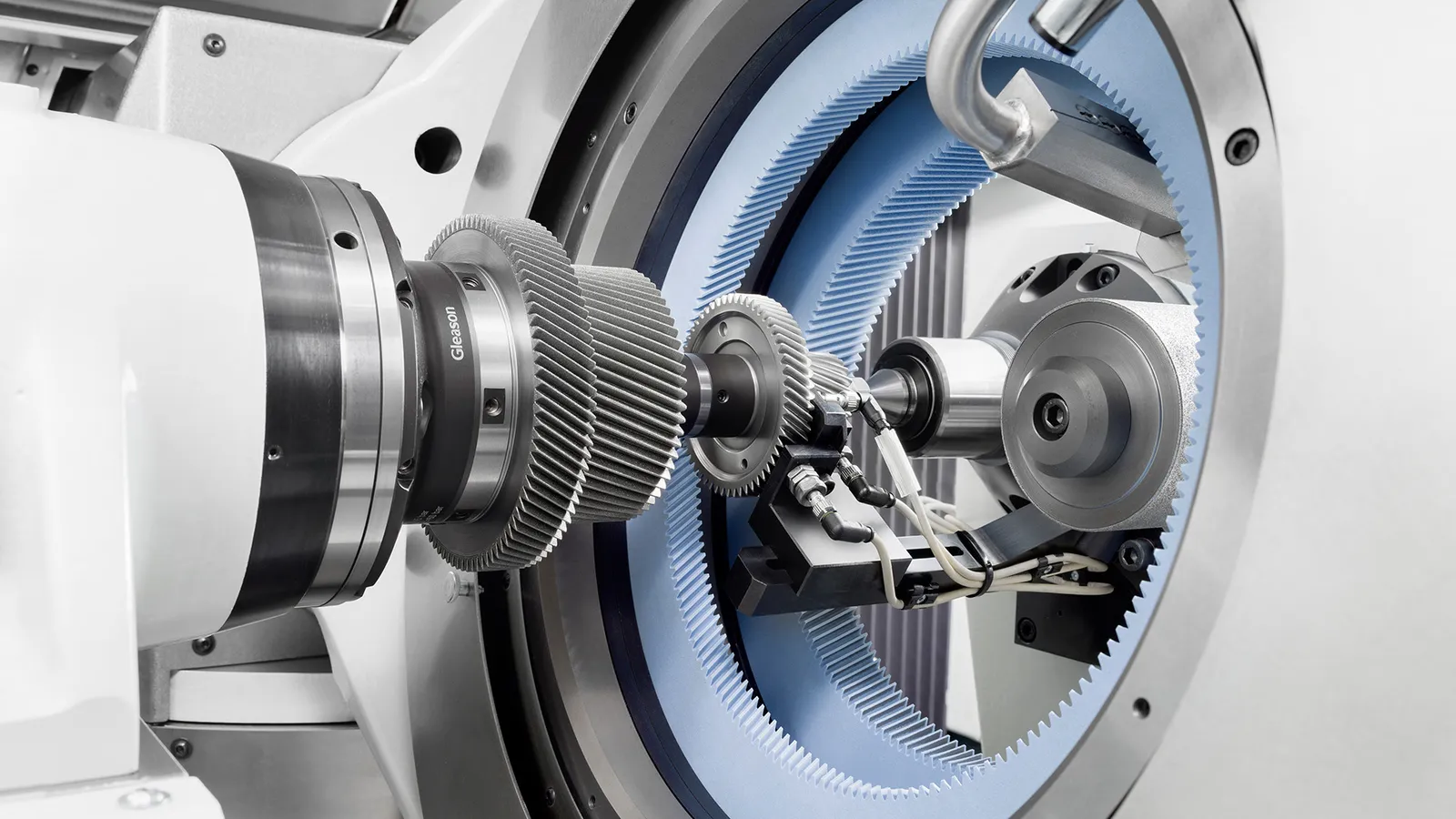
Gear Lapping: Final Finishing for Smooth Operation
Lapping is the final stage in gear finishing, where extremely low cutting force and abrasive slurry are used to polish the gear teeth and achieve optimal smoothness and contact pattern. This step ensures micro-adjustments in shape and increases operational life.
• Purpose: Surface cleanliness, micro-correction of shape
• Cutting Force: Very low (free-cutting with abrasive slurry)
• Stage: Final finishing
Further reading: Gear Lapping Process at PairGears
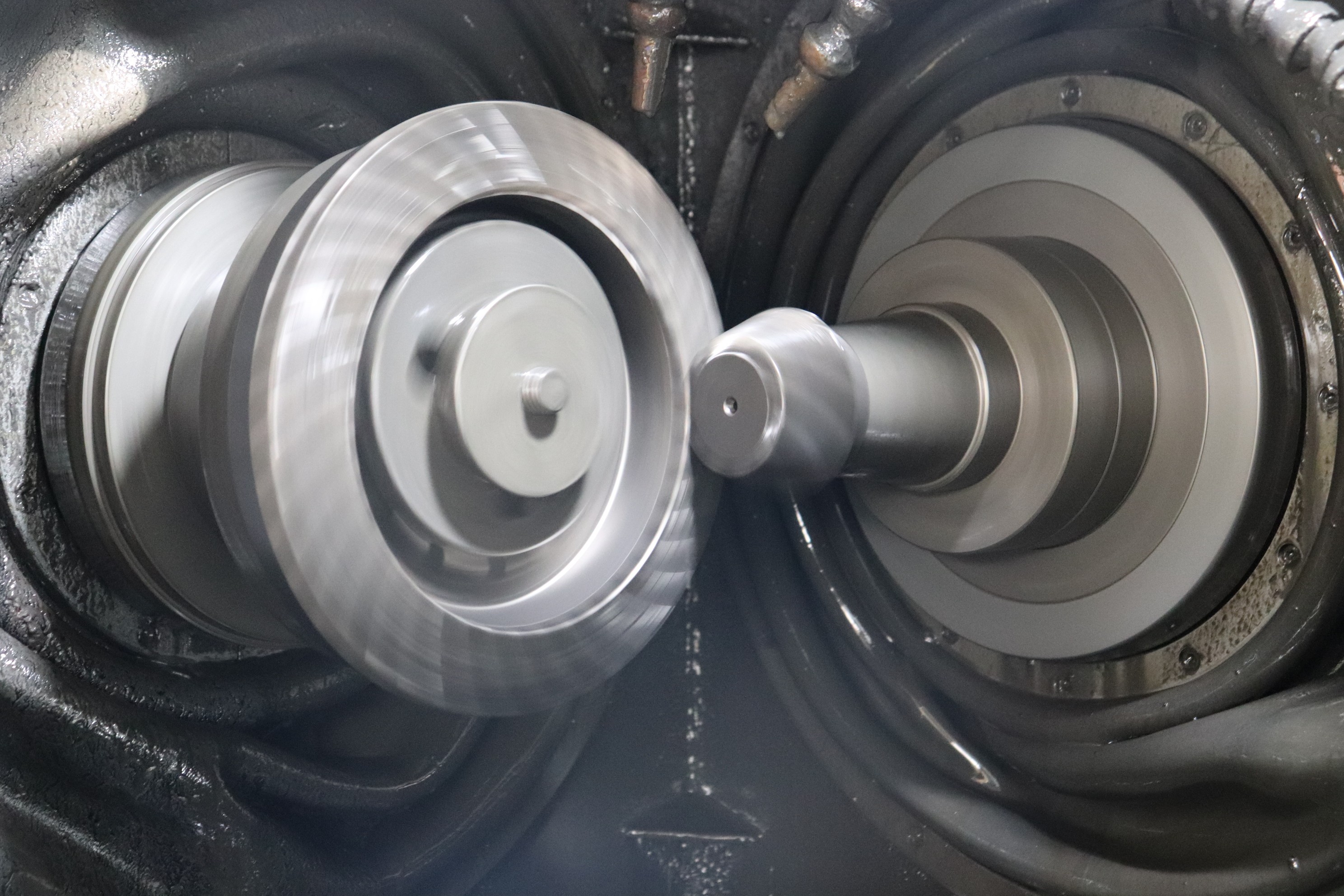
Integrating the Three at PairGears
At PairGears, we tailor each finishing process to the gear’s application and material characteristics. Grinding defines shape, honing improves functionality, and lapping ensures ultimate smoothness. By combining all three, we deliver gears that meet the highest performance standards.
Whether for agricultural machinery or truck gears, our finishing techniques ensure quiet, durable, and efficient gear systems.
Conclusion
Understanding the differences between gear grinding, honing, and lapping is essential for choosing the right manufacturing strategy. At PairGears, our mastery of these techniques allows us to deliver excellence in every gear we produce.
Should you have any questions or require further assistance, please do not hesitate to contact our engineer: ben@pairgears.com.