Understanding AGMA Standards: A Key to Gear Quality Control
Introduction to AGMA Standards in Gear Manufacturing
The American Gear Manufacturers Association (AGMA) plays a critical role in the development and maintenance of gear industry standards. These standards provide a set of rules and guidelines designed to ensure that gears meet specific performance, durability, and quality requirements. For gear manufacturers like PairGears, adhering to AGMA standards is crucial to guarantee the production of gears that meet the demanding needs of industries ranging from automotive and agriculture to construction machinery and electric vehicles.
This blog will explore the core AGMA standards and their significance in gear manufacturing. It will also discuss how these standards contribute to gear performance, reliability, and customer satisfaction.
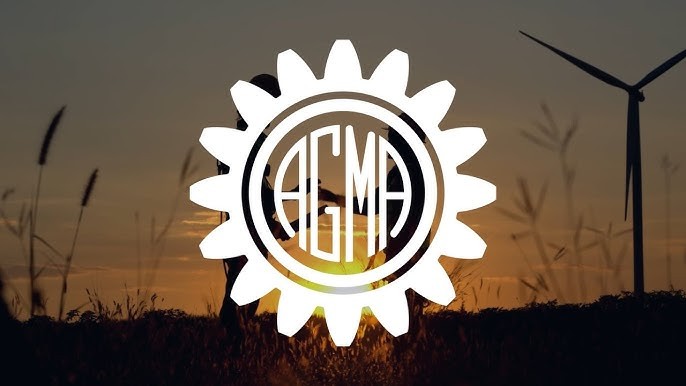
What Are AGMA Standards?
AGMA standards are a set of technical specifications developed by the American Gear Manufacturers Association to promote high-quality and efficient gear production. These standards address various aspects of gear design, manufacturing, and testing. The goal is to ensure that gears perform at their optimal level in diverse applications, ensuring long-lasting reliability and minimal maintenance.
Key AGMA Standards Relevant to Gear Quality Control
1. AGMA 2001—Gear Classification and Nomenclature
This standard provides the classification and naming system for different types of gears. It outlines the specific terminology used for gear shapes, dimensions, and configurations. Understanding this nomenclature helps manufacturers standardize gear specifications across the industry.
2. AGMA 9000—Gearbox Design and Performance
AGMA 9000 covers the design criteria for gearboxes, w
hich are often integral to larger gear systems. It includes requirements for gear ratio, torque capacity, and efficiency, ensuring that the gears perform optimally when assembled in gearboxes.
3. AGMA 2101—Fundamental Rating Factors for Rating Gears
This standard focuses on the fundamental principles for rating gears based on their load capacity and expected service life. It introduces formulas for calculating gear performance based on factors such as gear material, geometry, and operating conditions.
4. AGMA 508—Gear Inspection and Testing
Gear inspection is essential for ensuring that manufactured gears meet design specifications. AGMA 508 outlines the methods for testing gear accuracy, tooth profile, run-out, backlash, and other critical parameters. It provides procedures for both visual inspections and precision measurement tools.
5. AGMA 1104—Surface Finish and Lubrication
The surface finish and lubrication of gears directly affect their performance and longevity. AGMA 1104 outlines recommended practices for gear surface treatment, coating, and lubrication. This standard helps manufacturers optimize the performance of gears in high-load and high-speed applications.
6. AGMA 1202—Noise and Vibration Control in Gear Design
AGMA 1202 addresses the reduction of noise and vibration in gear systems. This standard covers the design and material choices that can mitigate undesirable noise and vibrations, enhancing the overall user experience.
Importance of AGMA Standards for Gear Manufacturers
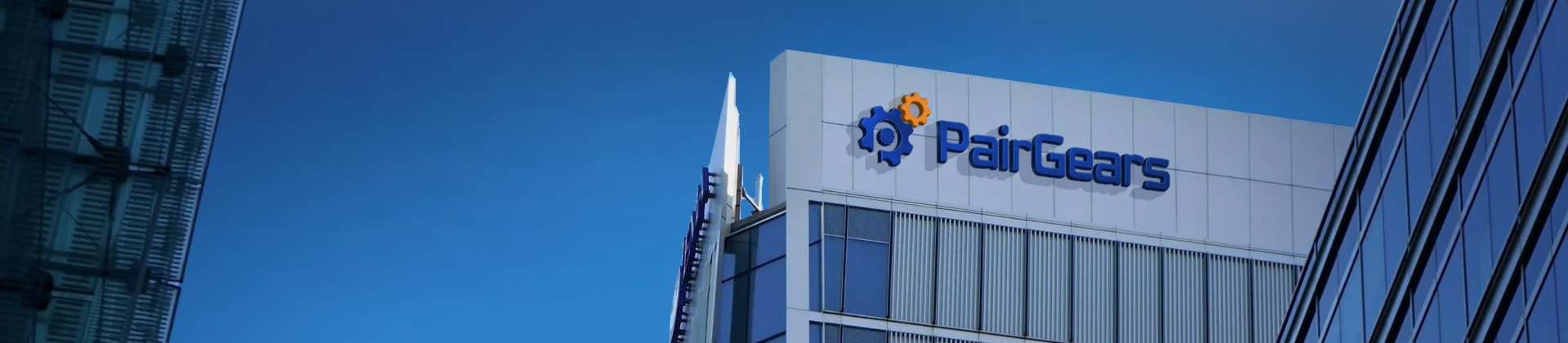
For manufacturers like PairGears, following AGMA standards is not just about compliance; it’s about ensuring the highest levels of gear precision, efficiency, and reliability. By adhering to these standards, gear manufacturers can:
· Ensure Consistent Quality: Following AGMA standards helps maintain consistency across production runs, minimizing defects and deviations from specifications.
· Increase Gear Longevity: Proper gear design and manufacturing, based on AGMA guidelines, result in longer-lasting gears that reduce the need for frequent replacements and maintenance.
· Improve Efficiency: Standardized processes help manufacturers optimize production times and reduce costs while maintaining high-quality standards.
· Meet Industry Requirements: Many industries, such as automotive and agriculture, demand that gears meet specific performance and quality benchmarks. AGMA standards ensure compliance with these industry-specific needs.
· Enhance Customer Satisfaction: Providing gears that are reliable and perform well in their intended applications enhances customer trust and loyalty.
PairGears and AGMA: Commitment to Excellence
At PairGears, we take pride in our commitment to producing high-quality gears that meet or exceed AGMA standards. Our team continuously monitors production processes to ensure that every gear we manufacture adheres to strict quality control procedures. This commitment extends to the materials we use, the design techniques we employ, and the testing processes we follow.
For instance, our Planetary Gears, Helical Gears, and Spur Gears are all produced with meticulous attention to AGMA standards. Whether it's gear tooth hardness, surface finish, or gear performance under load, we ensure that our products deliver optimal results for industries such as agriculture, construction, and automotive.
If you're interested in learning more about our products, check out our gear catalog.
How PairGears Implements AGMA Standards in Production
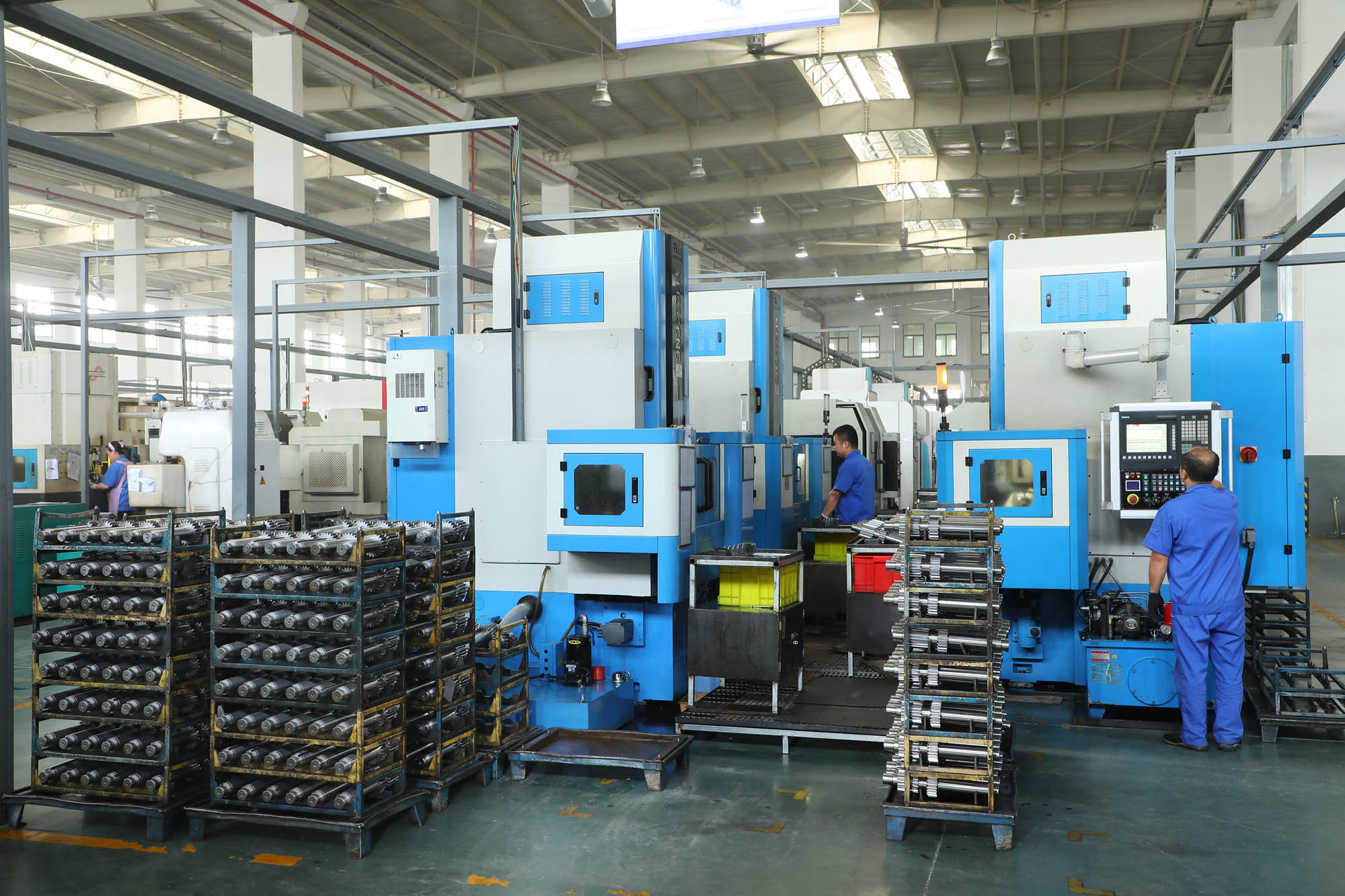
To meet AGMA standards, PairGears utilizes advanced manufacturing technologies and processes. Here’s how we ensure our gears comply with the best industry practices:
1. Design Process:
Our engineers design gears according to AGMA’s ratings and guidelines. This ensures optimal performance for each application, whether it's for agricultural machinery, trucks, or construction machinery.
We choose high-quality materials that meet AGMA’s criteria for strength, durability, and wear resistance. Materials like alloy steels and case-hardened materials are commonly used for their excellent mechanical properties.
We employ CNC machines and gear grinding equipment to achieve the precise tooth geometry and surface finish that AGMA standards demand. Our manufacturing processes are calibrated regularly to maintain this precision.
Every gear undergoes comprehensive inspection based on AGMA guidelines. This includes testing for tooth profile, backlash, run-out, and overall accuracy. Our team uses advanced measuring tools and visual inspections to ensure each gear meets the required specifications.
To improve gear life and performance, we apply the appropriate surface treatments and lubricants as recommended by AGMA standards. This helps reduce friction, wear, and noise in the final product.
Conclusion
In summary, AGMA standards are essential to ensuring the quality and performance of gears in a wide range of applications. As a trusted gear manufacturer, PairGears follows these rigorous standards to deliver products that exceed customer expectations. Whether you're looking for gearbox gears, planetary gears, or customized gears, you can count on us for high-quality, reliable, and long-lasting solutions.
Should you have any questions or require further assistance, please do not hesitate to contact our engineer: ben@pairgears.com.